Selecting the right poly welding machine is a crucial decision that can significantly impact the success and efficiency of your project. Whether you’re working in construction, plumbing, gas distribution, or any other industry that involves polyethylene (poly) pipes, choosing the appropriate machine ensures strong, durable welds that meet industry standards. This article will guide you through the key factors to consider when selecting the best poly welding machine for your specific needs.
1. Understand Your Project Requirements
Before diving into the technical details of poly welding machines, it’s essential to have a clear understanding of your project requirements. Consider the following questions:
What is the size and type of pipes you will be welding?
What is the scope and scale of your project?
Will the project involve fieldwork, or will it be conducted in a controlled environment?
What are the industry standards and regulations for the type of welding you’ll be performing?
Understanding these requirements will help you narrow down your options and focus on machines that are best suited for your specific project.
2. Types of Poly Welding Machines
There are several types of poly welding machines, each designed for different applications and pipe sizes. The three main types are:
Butt Fusion Machines: These are the most commonly used poly welding machines. They align and fuse the ends of pipes by applying heat and pressure. Butt fusion machines are ideal for large-diameter pipes and are widely used in gas and water distribution systems.
Electrofusion Machines: Electrofusion welding uses specialized fittings with built-in heating elements. The machine passes an electric current through the fitting, causing it to heat and melt the pipe surface, creating a strong bond. Electrofusion is particularly suitable for repairs and small to medium-diameter pipes.
Socket Fusion Machines: Socket fusion involves heating the outer surface of the pipe and the inner surface of a fitting, then joining them together. This method is common in plumbing and HVAC installations and is best suited for smaller pipes.
Each type of machine has its advantages and limitations, so choosing the right one depends on the specific requirements of your project.
3. Consider Pipe Size and Material
The size and material of the pipes you’ll be working with are critical factors in selecting a poly welding machine. Here’s what to consider:
Pipe Diameter: Ensure the machine can accommodate the range of pipe diameters you’ll be welding. Some machines are versatile and can handle a wide range of sizes, while others are designed for specific diameters.
Material Compatibility: While most poly welding machines are designed for polyethylene, some machines may be compatible with other thermoplastics. Ensure the machine you choose is suitable for the material you’ll be welding.
4. Evaluate Portability and Ease of Use
Depending on the nature of your project, portability may be an important factor. If you’re working on a job site that requires frequent movement or is in a remote location, a lightweight, portable machine will be beneficial. Additionally, consider the ease of use:
User-Friendly Controls: Look for machines with intuitive controls and clear instructions. This is especially important if the machine will be used by operators with varying levels of experience.
Training and Support: Consider whether the manufacturer offers training and technical support. This can be invaluable, particularly for complex machines or when working on critical projects.
5. Assess Power Requirements
Poly welding machines have different power requirements depending on their size and capabilities. Some machines are electric and require a stable power source, while others may be battery-powered or hydraulic. Consider the following:
Power Availability: Ensure that the job site has the necessary power infrastructure to support the machine. For remote locations, battery-powered or generator-compatible machines may be more practical.
Energy Efficiency: Energy-efficient machines can reduce operating costs, especially for large-scale projects that require continuous welding.
6. Evaluate Build Quality and Durability
A poly welding machine is a significant investment, so it’s essential to choose one built to last. Consider the following aspects of build quality:
Construction Materials: Look for machines made from high-quality, durable materials that can withstand harsh job site conditions.
Reputation of the Manufacturer: Choose machines from reputable manufacturers known for producing reliable, long-lasting equipment.
Warranty and Maintenance: Check the warranty offered by the manufacturer and whether they provide easy access to spare parts and maintenance services.
7. Budget Considerations
While it’s important to choose a machine that meets all your technical requirements, budget is also a key consideration. Poly welding machines can vary widely in price depending on their capabilities and features. Consider the following:
Initial Cost vs. Long-Term Value: While a cheaper machine may be tempting, consider the long-term value of investing in a high-quality machine that offers better performance, durability, and efficiency.
Operational Costs: Factor in the cost of consumables, maintenance, and energy use when calculating the total cost of ownership.
Financing Options: Some manufacturers or suppliers offer financing options, which can make it easier to invest in a higher-end machine.
8. Future-Proofing and Technological Advancements
The technology behind poly welding machines is continuously evolving, with advancements aimed at improving efficiency, precision, and ease of use. When selecting a machine, consider whether it offers:
Upgradeability: Machines that can be upgraded with new features or software can help you stay ahead of industry developments.
Data Logging and Quality Control: Some advanced machines offer data logging features that help you monitor and record weld quality, ensuring compliance with industry standards.
Conclusion
Selecting the best poly welding machine for your project requires careful consideration of various factors, from the type of welding required to the specific needs of your job site. By understanding your project requirements, evaluating the different types of machines, and considering factors such as portability, power requirements, and budget, you can make an informed decision that will lead to successful, high-quality welds. Investing in the right machine not only ensures the durability and reliability of your work but also enhances overall project efficiency.
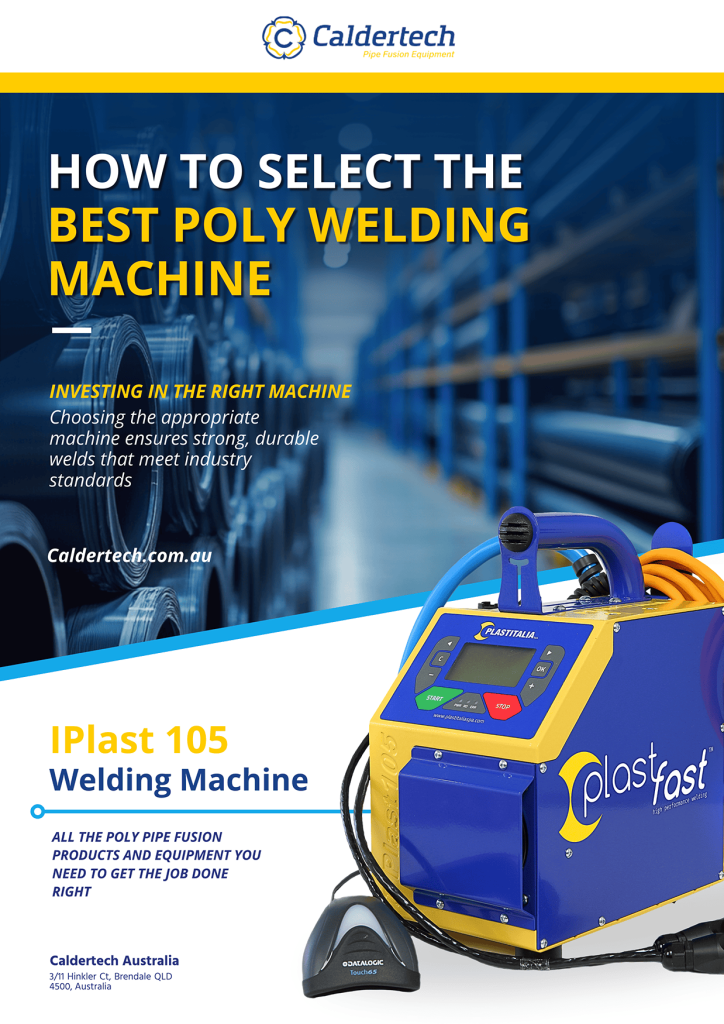